Cerakote vs Anodowanie
SPÓJNOŚĆ KOLORU
Cerakote
Wszystkie kolory Cerakote są zgodne ze standardem spójności kolorystycznej Delta E 1 lub mniej. Zazwyczaj ludzkie oko zauważa różnice w kolorach dopiero przy odchyleniu Delta E na poziomie 2 lub wyższym, co sprawia, że Cerakote jest doskonałym zamiennikiem anodowania dla wykończeń w dużych ilościach.
Anodowanie
Spójność kolorów często znacznie się różni między poszczególnymi elementami i partiami z powodu różnic chemicznych oraz subtelnych odchyleń w podłożu, które są trudne do kontrolowania.
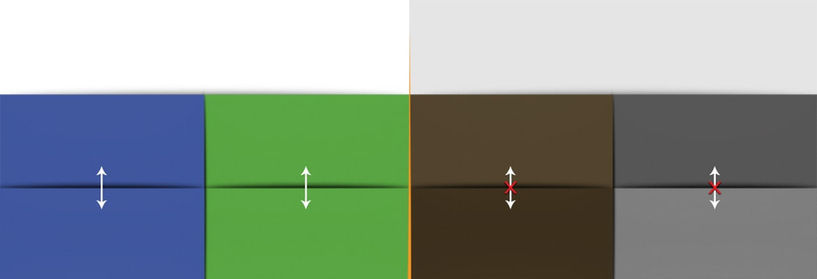
WPŁYW NA STOPY ALUMINIUM
Cerakote
Cerakote nie wpływa negatywnie na właściwości zmęczeniowe stopów aluminium.
Anodowanie
Spójność kolorów często znacznie się różni między poszczególnymi elementami i partiami z powodu różnic chemicznych oraz subtelnych odchyleń w podłożu, które są trudne do kontrolowania.

WPŁYW NA ŚRODOWISKO
Cerakote
Cerakote nie zawiera metali ciężkich i spełnia normy dotyczące lotnych związków organicznych (VOC) we wszystkich 50 stanach USA. Ponadto, powłoka Cerakote jest zgodna z regulacjami REACH, RoHS oraz Proposition 65.
Anodowanie
Proces anodowania za pomocą kwasu chromowego uwalnia chrom sześciowartościowy, silny czynnik rakotwórczy, do środowiska. W rezultacie stosowanie chromu sześciowartościowego jest coraz bardziej ograniczane przez przepisy.

Cerakote vs Oksydowanie
Przetestowaliśmy powłokę Cerakote i tradycyjne oksydowanie, zostawiając dwa karabiny z zamkiem czterotaktowym na 15 miesięcy na zewnątrz, w warunkach panujących na północno-zachodnim wybrzeżu Pacyfiku.
Dokumentowaliśmy, co się działo, robiąc codzienne zdjęcia za pomocą kamery z funkcją poklatkową. Oba karabiny były identyczne, z wyjątkiem tego, że jeden był pokryty Cerakote, a drugi miał oryginalne, tradycyjne oksydowane wykończenie. Zobacz, co się stanie:
Cerakote vs Korozja
Cerakote zostało poddane bezpośredniemu testowi w komorze solnej razem z innymi konkurencyjnymi powłokami, aby sprawdzić, jak długo wytrzymają, zanim ulegną korozji. Obejrzyj test i zobacz wyniki:
W kontekście powłok ochronnych dla broni palnej duży nacisk kładzie się na kilka kluczowych kategorii wydajności, takich jak:
-
Twardość
-
Odporność chemiczna
-
Smarowność
-
Odporność na ścieranie
-
Kolor
-
Jednak żadna z tych cech nie jest tak istotna jak ochrona przed korozją. Przeciętny właściciel broni zmaga się z korozją częściej niż z jakimkolwiek innym problemem związanym z powłokami. Zobaczysz, co się dzieje, gdy Cerakote zostaje wystawione na bezpośrednie porównanie w komorze solnej z siedmioma konkurencyjnymi powłokami. Która powłoka przetrwa najdłużej?
Testy NIC są zgodne z normami ASTM. ASTM International to uznany globalnie lider w tworzeniu norm, które poprawiają jakość produktów, bezpieczeństwo i zaufanie konsumentów. Według normy ASTM B117-03, test korozji zapewnia kontrolowane środowisko korozyjne, które umożliwia uzyskanie informacji o względnej odporności na korozję próbek metali i powlekanych metali w danej komorze testowej.
Komora solna jest ustawiona na temperaturę 95°F (ok. 35°C) przy 5% stężeniu soli. Testowanie w komorze solnej pozwala na porównanie metali i powłok, ale nie odnosi się bezpośrednio do konkretnej liczby godzin użytkowania w rzeczywistych warunkach. W sumie dziewięć komponentów broni zostaje umieszczonych w komorze solnej, aby sprawdzić, jak długo każda powłoka wytrzyma przed pojawieniem się pierwszych oznak korozji. W tym momencie dla danej powłoki zostanie odnotowany czas. Należy zauważyć, że nie wszystkie testowane komponenty są identyczne. W celu uzyskania jak najdokładniejszych wyników testowych, elementy z gotowymi powłokami zostały pozyskane bezpośrednio od producenta, jeśli były dostępne. Komponenty wymagające aplikacji, w tym Cerakote, zostały nałożone na przecięte sekcje tej samej lufy ze stali miękkiej, co zapewniło jednolity materiał bazowy dla wszystkich testowanych próbek, gwarantując dokładne porównanie.
Aby pokazać, jak surowe są warunki w komorze, jako punkt odniesienia umieszczono w niej lufę wykonaną z wysokiej jakości stali nierdzewnej 416. Środowisko w komorze solnej jest na tyle trudne, że uniemożliwia wykonanie wyraźnych zdjęć. Kamera została zamontowana na suficie nad komorą, a technik laboratoryjny otworzy drzwi komory, aby zrobić zdjęcia. Komora solna będzie działać tak długo, aż każda z powłok ochronnych wykazywać będzie oznaki korozji.
Która powłoka przetrwa najdłużej? Rdza pojawiająca się na białych panelach trzymających każdy element niekoniecznie wskazuje na pierwsze oznaki korozji. Komora solna recykluje wodę solną, która zbiera rdzę z atmosfery i osadza ją na powierzchniach w całej komorze testowej, co może dawać fałszywe wrażenie, że korozja już się rozpoczęła. Pierwsze oznaki korozji są odnotowywane, gdy testowane komponenty wykazują liczne obszary korozji pochodzącej z nierozłożonej rdzy. Test rozpoczyna się teraz…
Oksydowanie i stal nierdzewna wykazały widoczne oznaki korozji w ciągu pierwszych 24 godzin. Korozja była widoczna w ciągu pierwszych 48 godzin na powłokach FailZero, NIBX, Ionbond, Fosforan i KG Gun Kote. Zapis wideo został przyspieszony.
Po 172 godzinach Duracoat® zaczął wykazywać oznaki korozji. Zapis wideo ponownie przyspieszono.
Teraz wyraźnie widać, która powłoka ochronna wytrzymuje dłużej niż pozostałe.
Test zakończono ostatecznie po 2034 godzinach, kiedy Cerakote wykazał pierwsze oznaki korozji. Wyniki ochrony przed korozją są przedstawione na prostym wykresie słupkowym, który pokazuje powłoki ochronne na jednej osi oraz czas i godziny na drugiej. Zgodnie z normą ASTM B117-03, Cerakote zakończył test z wynikiem przeszło 11 razy lepszym od najbliższej konkurencyjnej powłoki i 85 razy dłuższym od standardowego oksydowania lub stali nierdzewnej.
Kiedy ochrona przed korozją ma znaczenie, wybierz Cerakote i Finish Strong™.
Cerakote vs Temperatura
Gdy liczy się wydajność, wygląd i stabilność temperaturowa, tylko jedna powłoka zdobywa podium we wszystkich trzech kategoriach jednocześnie. Wysokotemperaturowe powłoki Cerakote są idealnym rozwiązaniem dla części takich jak układy wydechowe, kolektory, turbosprężarki i kolektory wlotowe.

Cerakote vs Black Nitride by CVA®
Umieściliśmy dwie lufy w komorze solnej, aby sprawdzić, która powłoka okaże się bardziej wytrzymała. Jedna była wykończona powłoką antykorozyjną Black Nitride od CVA®, a druga pokryta Cerakote. Obejrzyj i zobacz, kto wygra ten pojedynek:
To jest test odporności na korozję przeprowadzony na dwóch lufach od wiodących producentów broni palnej. Lufa na dole ekranu to lufa ze stali nierdzewnej 416, fabrycznie zabezpieczona powłoką antykorozyjną Black Nitride od CVA®. Lufa u góry jest wykonana ze stali miękkiej i fabrycznie zabezpieczona ceramiczną powłoką Cerakote od Traditions™ Performance Firearms. Obie lufy umieszczono w komorze solnej o temperaturze 95°F i stężeniu soli 5%, zgodnie ze standardem testowym ASTM B117.
Test rozpoczyna się teraz. Komora solna to kontrolowane, korozyjne środowisko, które wystawia próbki na działanie ogrzewanej pary solnej, przyspieszając proces korozji.
Zaledwie po 8 godzinach od rozpoczęcia testu, lufa zabezpieczona powłoką Black Nitride od CVA® wykazuje oznaki korozji. Materiał filmowy został przyspieszony.
Wreszcie, Cerakote wykazuje pierwsze oznaki korozji po 1 206 godzinach. Lufa od Traditions™ Performance Firearms, chroniona powłoką Cerakote, wytrzymała 150 razy dłużej bez widocznych oznak korozji niż lufa z powłoką Black Nitride od CVA®.
Ten materiał wideo pokazuje, że gdy liczy się ochrona przed korozją, Cerakote przewyższa i przetrzymuje konkurencję, czyniąc ją oczywistym wyborem.
Finish Strong™ z Cerakote.
Cerakote vs Powłoki PVD/DLC
Zarówno producenci, jak i klienci oczekują najwyższej jakości wykończeń. Ekspozycja na środowiska korozyjne, zużycie i ścieranie oraz działanie agresywnych substancji chemicznych negatywnie wpływają na części i wyroby gotowe. Ceramiczne powłoki Cerakote stanowią doskonałe ulepszenie oraz świetną alternatywę dla powłok PVD (fizyczne osadzanie z fazy gazowej), Ionbond oraz powłok DLC (diamond-like carbon).
Cerakote to innowator w technologii ceramicznych powłok, oferujący niezrównaną ochronę przed korozją, odporność chemiczną i odporność na ścieranie – wszystko to w ultracienkiej, ceramicznej powłoce. Cerakote można nakładać na większość powierzchni i oferuje setki różnych opcji kolorystycznych. Cerakote jest łatwo nakładany zarówno ręcznie, jak i automatycznie, w prostym procesie jednowarstwowym (nie wymaga ani warstwy podkładowej, ani nawierzchniowej).


ODPORNOŚĆ CHEMICZNA
Ekstremalna odporność chemiczna Cerakote chroni twoje komponenty nawet w najtrudniejszych warunkach. Cerakote zachowuje swój kolor i właściwości po ekspozycji na takie chemikalia jak:
-
Środki do czyszczenia broni
-
WD-40®
-
Środek do czyszczenia hamulców
-
Alkohol skażony
-
Rozcieńczalnik do lakieru
-
Metylowy etyloketon (MEK)
-
Aceton
-
Benzyna
-
Diesel
-
Benzyna lakowa
-
Środek do usuwania farb
-
Roztwór 5% HCL
-
Wybielacz
-
Drano®
-
Środki czystości domowej
-
Środki dezynfekujące
Cerakote vs Teflon ® I Xylan®
W środowiskach przybrzeżnych i morskich ochrona przed korozją oraz wydajność są kluczowe dla elementów takich jak łączniki, śruby, gwinty i inne. W tych zastosowaniach istotna jest nie tylko niska tarcie, ale także ochrona antykorozyjna. Uznając Cerakote za idealne zastępstwo lub alternatywę dla powłok PTFE, postanowiliśmy przetestować nasz produkt w porównaniu z innymi standardowymi powłokami stosowanymi w branży.
Powłoka Cerakote E-100 Blackout została przetestowana pod kątem odporności na korozję w porównaniu z powłokami Teflon® Black 958G, Teflon® Metallic Black 420G oraz Xylan® 142X, stosowanymi w aplikacjach morskich do ochrony przed korozją. Wszystkie powłoki zostały nałożone na zwykłe stalowe śruby i nakrętki cynkowane w celu zwiększenia tempa korozji galwanicznej.
Analiza została przeprowadzona w komorze solnej Q-Fog zgodnie z normą ASTM B117, a ocena stopnia korozji opierała się na normie ASTM D610. Wszystkie powłoki nałożono na śruby i nakrętki sześciokątne powszechnie stosowane w przemysłowych środowiskach morskich. Standard Cerakote dotyczący awarii korozyjnej to poziom rdzy 5-G, czyli 3% powierzchni pokrytej rdzą.
Cerakote E-100 Blackout znacznie przewyższa ochronę antykorozyjną wiodącego konkurenta, zapewniając ponad 3 470 godzin dodatkowej ochrony. Cerakote dąży do dostarczania branżom najwyższej jakości rozwiązań powłokowych, niezależnie od zastosowania. Ten test pokazuje, że gdy ochrona przed korozją ma znaczenie, Cerakote jest najlepszym wyborem.

Cerakote to wiodąca powłoka ochronna, której zaawansowana technologia oferuje niezrównaną ochronę przed korozją, odporność chemiczną i wytrzymałość na ścieranie, idealna dla zastosowań przemysłowych, w tym także do personalizacji broni. W testach na odporność na korozję, Cerakote E-100 Blackout przewyższa standardowe powłoki, takie jak Teflon® i Xylan®, o ponad 3 470 godzin, pokazując, że jest to najlepszy wybór do długotrwałej ochrony w ekstremalnych warunkach.
Malowanie Cerakote, dostępne w Weapon-Wizards.com, to idealna opcja dla właścicieli broni, którzy cenią wytrzymałość i styl. Dzięki doskonałej odporności Cerakote na substancje chemiczne i korozję, powłoka ta stanowi idealną alternatywę dla tradycyjnych powłok PVD i DLC, szczególnie w wilgotnych środowiskach, takich jak wybrzeża i obszary morskie.
Usługi Cerakote Kraków w Weapon-Wizards.com oferują profesjonalne malowanie broni oraz personalizację, dzięki czemu klienci mogą uzyskać unikalny wygląd swojej broni z setkami opcji kolorystycznych. Malowanie Cerakote to proces jednowarstwowy, który zapewnia doskonałą ochronę bez potrzeby stosowania dodatkowych powłok podkładowych i nawierzchniowych, co czyni go idealnym wyborem do ochrony broni i innych metalowych powierzchni.
Podsumowując, Cerakote to powłoka, która oferuje najwyższy poziom ochrony antykorozyjnej, wytrzymałości i estetyki. Gdy poszukujesz „Malowanie Cerakote” lub „personalizacja broni” w Krakowie, Weapon-Wizards.com to miejsce, które gwarantuje najwyższą jakość i trwałość powłok ochronnych.